Sign Up for News Updates
Few things in life are guaranteed. That’s where energy service companies (ESCOs) come in.
ESCOs operate on an intriguing premise: They can analyze a facility’s energy performance and recommend upgrades to achieve savings that will, in effect, fund said upgrades — guaranteed.
Here’s how it works: An organization and an ESCO enter a performance contact wherein funds for infrastructure improvements are secured through energy cost savings gleaned from high-efficiency HVAC systems, LED lighting, solar panels, and other measures the ESCO proposes. These are long-term contracts during which the ESCO monitors the building’s energy consumption over 10, 15 or 25 years to ensure the projected savings are met.
ESCOs coordinate with existing contractors, engineers and architects who may be familiar with the building’s operational characteristics and needs.
For organizations that do not have immediate access to capital, an ESCO can be a smart alternative, if not their only option. That’s why ESCOs primarily work for public institutions, which are often tasked with meeting strict energy mandates but lack the cash for needed improvements.
“Mandates drive the industry,” says Timothy Unruh, Ph. D, P.E., CEM, LEED-AP, executive director of the National Association of Energy Services Companies. “So, the building owners have to figure out how they’re going to reduce energy consumption by X and still meet their budget.”
Because taxpayers won’t likely vote for, say, a new boiler room for a county building, government agencies tap ESCOs to find ways to fund energy-efficient retrofits.
It’s a growing field, as more buildings pursue LEED certification and zero-net-energy performance. In other cases, the practical reality of malfunctioning equipment and poor occupant comfort spur an ESCO project. Such was the case with Shepherd University.
College goes all in on ESCO
Shepherd University is a state university in Shepherdstown, West Virginia. Because student fees fund infrastructure improvements, the school didn’t have the resources for sorely needed mechanical upgrades.
The university contracted CMTA to audit the campus for its biggest pain points. The mechanical-electrical-and-plumbing engineering firm identified four buildings overdue for renovations, beginning with the Butcher Athletic Center, the campus’ largest energy offender. Built in 1989, the 80,000-square-foot facility still relied on its original HVAC equipment of split system air conditioning with electric heat strips and a large, packaged rooftop unit that ran 24 hours a day lest it fail to overcome temperature differentials between cycles.
“The majority of it had failed,” says John Goodin, CMTA’s principal engineer and project manager. “It probably didn’t work from the start, to be honest with you, because they had these big split-system air handlers that had really long line lengths.”
CMTA overhauled the facility’s space heating, installing a four-pipe hydronic HVAC system with an air-cooled chiller and a central plant of condensing boilers served by two 1,000-gallon underground propane tanks. The building also has a new automation system and controls, and a dedicated rooftop air handling unit serving the gym.
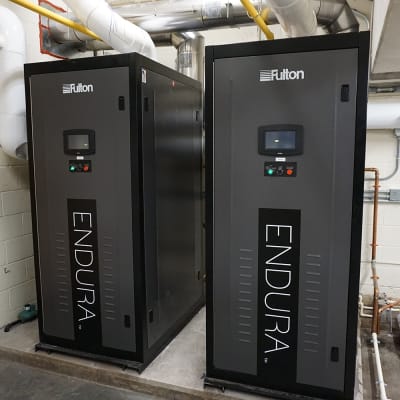
CMTA replaced the gym’s old oil-fueled boilers with two propane-fired condensing boilers that serve the facility’s hydronic HVAC system.
When it came to considering a heat source, CMTA and university officials weighed their options. Shepherdstown is out of reach of the nearest natural gas supplier, and heating oil was deemed too pricey. They considered a geothermal heat pump system, but the region’s geography wasn’t ideal. Plus, they determined such a system would not accommodate the building’s zoning – the method of supplying different temperatures to areas of a building. That’s how they landed on a clean-burning alternative fuel.
“Propane made a lot of sense for heating a big gym building,” Goodin says.
Crunching the numbers
ESCOs use an Energy Use Intensity (EUI) score, which measures a building’s annual energy consumption per square foot of floor space, to establish a baseline performance measure. Based on existing utility bills, CMTA calculated that the Butcher Athletic Center operated at a pre-project EUI of 66 kBtu a year.
“Propane made a lot of sense for heating a big gym building”
Goodin didn’t anticipate that the number would change much with the energy improvements. That’s because half of the old HVAC equipment didn’t work, resulting in an artificially low EUI. With a new, fully operational system, Goodin figured the number would remain roughly the same. So, he was surprised when CMTA came back with a post-project EUI of 47.5. That equals a total energy cost savings of $45,392 a year.
“We didn’t think it would be much of an energy savings proposition … but we effectively decreased their utility bills by 31 percent in their first year,” Goodin says.
The savings go beyond lower energy costs. Goodin estimates the school was spending $30,000 to $50,000 in annual HVAC repairs. That’s more money that can fund additional improvements.
The renovated gym is the first phase of a $6.5 million project that guarantees more than $400,000 in annual energy savings across the campus with an ROI within 15 years.