Sign Up for News Updates
More than two million people a year come to experience the spires, pinnacles, slot canyons, and caves of Bryce Canyon, Utah. Many of them expect hot showers — an accommodation the primary lodging facility serving park visitors couldn’t always guarantee.
Ruby’s Inn used to issue refunds to the tune of $60,000 a year due to hot-water issues. These days, refunds are a rarity. Instead of giving money back to disgruntled guests, the property is saving a significant amount of cash, while sparing the environment 5,200 metric tons of carbon annually, thanks to an overhaul of its hot water system and continued reliance on propane, a low-carbon fuel. To put that in perspective, 5,200 metric tons is equivalent to greenhouse gas emissions from 1,410 gas-powered passenger vehicles for a year.
For this reason, the Propane Education and Research Council honored Ruby’s Inn management with the Energy for Everyone Hero Award as the historic lodge continues to make strides toward a lower-carbon future.
Transitioning to tankless
Where there were clunky, unreliable and grossly inefficient open-flame boilers struggling to heat thousands of gallons of stored water around the clock, there are now sleek, efficient, on-demand tankless water heaters — 183 of them to be exact – fueled by propane.
The $750,000 upgrade was well worth the investment, says Ruby’s Inn general manager Lance Syrett, and not just to quell the complaints. From an environmental standpoint, it was the right thing to do. Propane-fueled tankless water heaters, such as the Rinnai units used in the Ruby’s Inn project, reduce carbon emissions by up to 50 percent compared with electric storage systems.
“We always remind the [park] superintendents that we’ve been good stewards of Bryce Canyon National Park longer than Bryce Canyon has been a national park,” Syrett says. (Syrett’s great grandfather, Ruben Syrett, established a “tourist rest” near the brink of Bryce Canyon before the site became a National Monument and later a National Park.)
Today, Ruby’s Inn comprises 19 buildings, 700 hotel rooms, three restaurants, a carwash, three swimming pools and spas, plus employee housing. Two propane tanks totaling 48,000 gallons fuel much of this infrastructure: water and space heating, backup generators, cooking equipment, and even a laundry facility handling 19 tons of laundry a day. Among some recent investments the property has made are a 1.3 million Btu flat-iron press that steams and folds about 15 sheets per minute and an ice-melt system. These are also powered by propane.
Curbing consumption
“We don’t believe Ruby’s Inn would be what it is today if it wasn’t for using propane,” says Ron Harris, the property’s health and safety manager.
Being so remote, natural gas isn’t an option and fuel oil is too dirty. Going all-electric isn’t a possibility, either.
“They don’t have enough electricity in the grid to run a site like this, not this remote,” says Jim Bunsey, director of commercial business development at the Propane Education and Research Council (PERC). Besides, propane is a greener energy source. “We may be a fossil fuel, but we burn cleaner than the grid does today,” he adds.
With propane, the facility can maintain operations more reliably while curbing emissions. Even as the property continues to invest in more propane-fueled equipment, fuel consumption has dropped due to advancements in technology. Ruby’s Inn chief engineer, Karl Munford, says the facility has cut gallonage from 425,000 thousand to 380,000 last year. He attributes much of those savings to the 199 Btu Rinnai tankless units which operate at 97 percent efficiency rating.
“What I think the Ruby’s Inn project exemplifies is the power of the propane industry to provide technology and solutions that really make a tremendous difference in the operation of a business like this,” says Jeff Steward, owner of Blue Star Gas. “Propane can do in this in metropolitan areas, and it can do this in the most rural areas.”
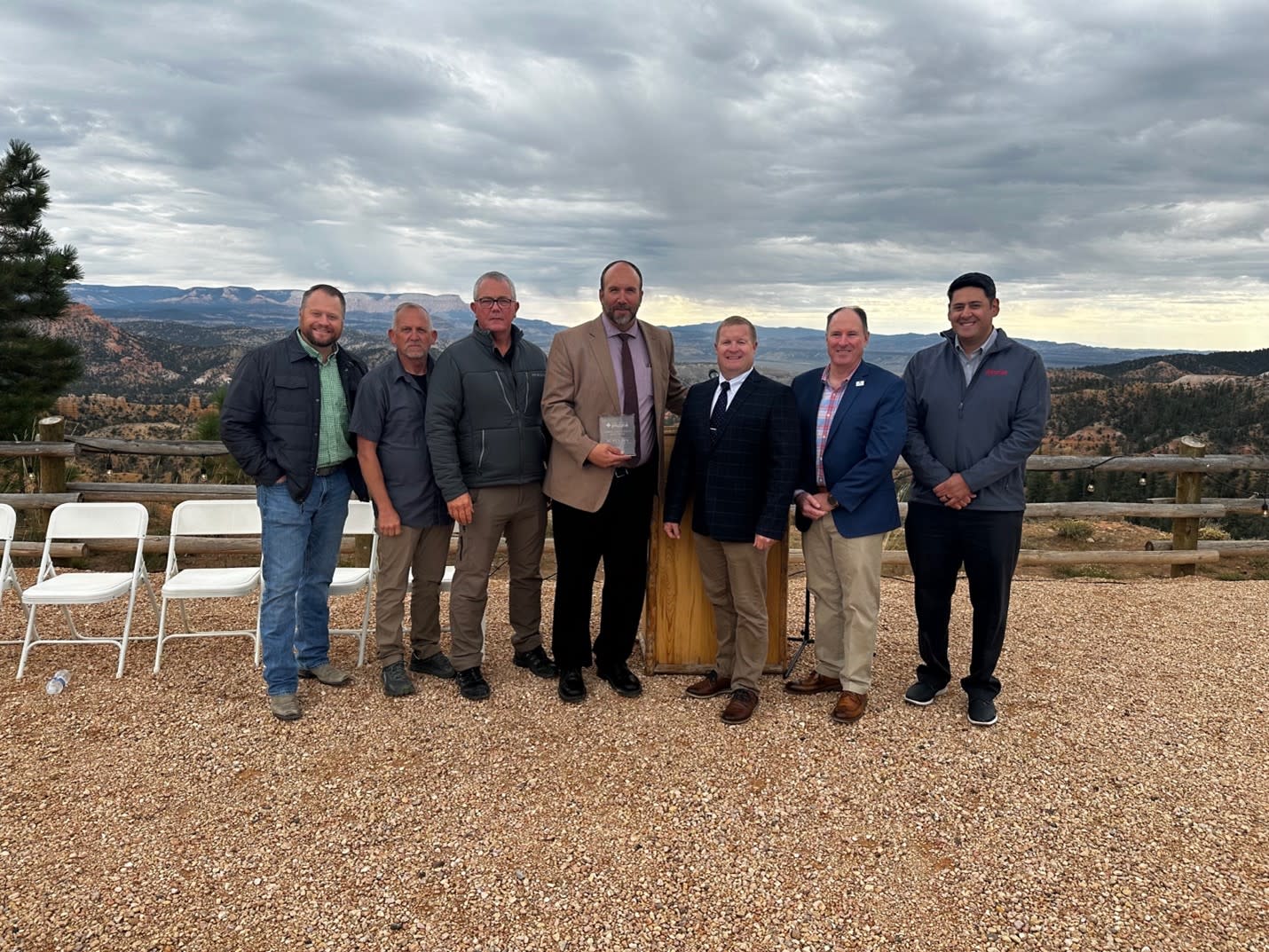
In September, PERC honored Ruby’s Inn management with the Energy for Everyone Hero Award for their ongoing commitment to lowering the facility’s carbon footprint. From left, Brannon Morse of Kiva Energy, Karl Munford, Ruby’s Inn chief engineer, Ron Harris, Ruby’s Inn health and safety manager, Lance Syrett, Ruby’s Inn, general manager, Jim Bunsey, PERC’s director of commercial business development, Jeff Stewart, owner Blue Star Gas, Michael Prayoonvech, systems design engineering manager at Rinnai.
Future projects will slash emissions further. Property managers are currently exploring a community propane system wherein a collection of modular homes used by employees would connect to a single propane tank fueling efficient space and water heating equipment. Renewable propane is another possibility on the horizon. Ruby’s Inn could make an easy switch to low- to negative- carbon intensity fuel on their path to zero. All existing propane infrastructure on the property is compatible.